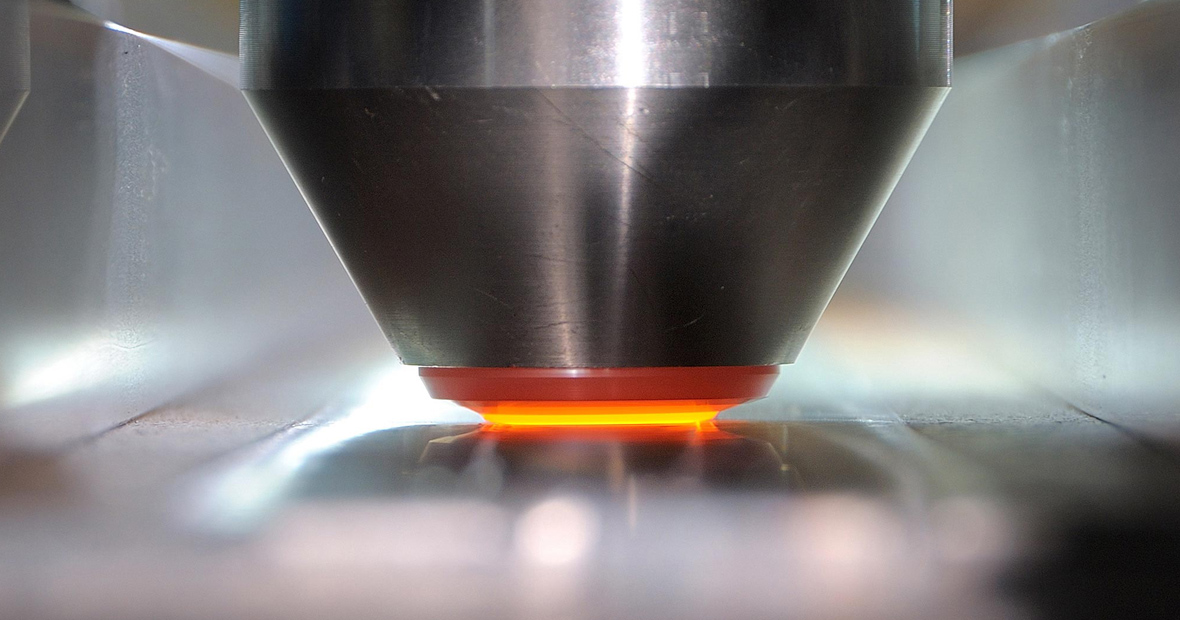
Delving into the world of friction stir welding (fsw) products, manufacturers are presented with a plethora of choices. With each decision comes its own set of considerations, from material compatibility to tool design, process parameters, and equipment selection. Mastering the art of fsw involves understanding these aspects in depth and leveraging them to achieve optimal welding results. The focus here rests squarely on evaluating material compatibility, understanding the influence of tool design, assessing mechanical and thermal properties, and optimizing process parameters, all while navigating the selection of effective fsw equipment. This presents a comprehensive guide, considering all these aspects, to aid manufacturers in making well-informed decisions on the right fsw product.
Evaluating material compatibility for friction stir welding
Manufacturers often face challenges when choosing the right friction stir welding product. Compatibility between materials is a key aspect to consider in order to achieve a successful friction stir welding (FSW) process. The selection criteria for suitable FSW materials include aluminum, steel, and copper.
Factors Influencing Material Selection in FSW
Thermal compatibility plays a significant role in the FSW process. The heat generated during the welding process can affect the property of the materials. Thus, understanding this aspect is vital for achieving a successful FSW weld. Moreover, the heterogeneity of the materials can impact the quality of the weld in FSW. Hence, selecting materials with similar thermal properties can lead to better welding outcomes.
Comparing Aluminum, Steel, and Copper in FSW Applications
Each material has its own advantages and limitations when it comes to FSW. For instance, aluminum alloys are commonly used due to their good formability and thermal conductivity. On the other hand, steel and copper, despite their high strength and excellent electrical conductivity, respectively, pose certain challenges due to their high melting points.
Overcoming Challenges with High-Strength Alloys in FSW
High-strength alloys can be difficult to work with in FSW due to their high melting points and strength. However, with continuous advancements in FSW technology, potential solutions are being developed to tackle these challenges. One such advancement is the ability to join dissimilar materials, marking a significant leap from innovation to industrial application.
Understanding the influence of tool design on fsw quality
Manufacturers must give due consideration to the selection of friction stir welding (FSW) products to ensure optimal welds. Every aspect of tool design, from shape and size to material choice, plays a significant role in the welding process and ultimately affects the quality of the weld.
Choosing the Right Tool Shape and Size for Optimal Welds
The design of the threaded pin is crucial for optimizing penetration and dispersion of material during FSW. An appropriately designed threaded pin facilitates efficient material mixing, which is integral to forming a robust joint. Moreover, the tool's tilt angle significantly influences material flow control, thereby reducing welding defects. Hence, understanding the relationship between tool geometry and material mixing efficiency is vital.
Impact of Tool Material on Weld Durability and Strength
Tool design also affects tool durability and longevity in repetitive FSW processes. Material choice for the tool impacts the tool's lifespan and the durability of the weld. Therefore, it is essential to adapt the tool design to the specific material requirements to maximize weld quality and strength.
Advanced Tool Features : Threaded Pin and Shoulder Designs
The choice of shoulder design influences the formation of the thermally affected zone and weld quality. Advanced features like a well-designed shoulder ensure a lower thermally affected zone, leading to a higher quality weld. The threaded pin and shoulder designs are therefore key considerations in FSW tool design to ensure optimal weld quality.
Assessing mechanical and thermal properties of fsw joints
Manufacturers engaging with friction stir welding (FSW) products must take into consideration multiple factors for a successful operation. One of these considerations includes the tensile strength properties of FSW joints, which vary depending on the alloys utilized. Different alloys yield different results, hence, choosing an alloy that ensures high tensile strength is imperative. Another key factor is the evaluation of FSW welding parameters' impact on the joints' micro-hardness. A deep understanding of these parameters allows manufacturers to control the hardness of the FSW joints effectively.
Manufacturers should be aware of thermal variations within FSW joints. These variations directly affect the final mechanical properties of the joints. Therefore, controlling these variations is essential to achieve the desired mechanical properties. Furthermore, manufacturers must identify factors influencing the formation of defects and their impact on lap joint strength. Defects can drastically reduce the strength of the lap joint, hence, their prevention is vital. There exists a correlation between FSW welding speed and the thermal distribution within the joints, which should be taken into consideration. Lastly, the effect of the thickness of the welded materials on the joint strength, measured in MPa, and the joint hardness, is another crucial factor. The thickness directly influences these properties, thus, selecting the appropriate thickness is critical to achieve the desired results.
Optimizing process parameters for enhanced weld strength
Manufacturers seeking to maximize the strength of their welds and minimize defects should give serious consideration to the optimization of their process parameters. The speed at which the weld is executed plays a significant role in the quality and strength of the resultant joint. A slower speed may result in a stronger weld, but at the cost of increased heat in the thermally affected zone. Conversely, a higher speed can reduce the heat impact but may lead to a weaker joint. Therefore, finding the right balance is essential.
Temperature control techniques are another critical element in achieving strong, defect-free welds. Excessive heat can weaken the areas adjacent to the weld, compromising the structural integrity of the entire assembly. Selecting the optimal tools and materials can help in this regard, as can adjusting pressure parameters to improve the cohesion and durability of the welded joints. The ideal friction stir welding product can aid in these efforts.
For high-strength applications, manufacturers should consider adopting tailored strategies for process optimization. These strategies could include elements such as variable speed control, dynamic pressure adjustment, and advanced heat management. With the right approach, it is possible to achieve welded joints of exceptional strength and durability, with minimal defects and thermal impact.
Navigating the selection of fsw equipment for manufacturing efficiency
Understanding the essentials of FSW lays the groundwork for enhancing manufacturing efficiency. A thorough grasp of the process, and the benefits it brings to manufacturing efficiency, is indispensable. The selection of FSW equipment hinges on three key criteria - performance, reliability, and adaptability to a variety of materials. A careful selection process leads to significant cost reductions in production and improves the quality of components manufactured using this method.
Recent innovations in the FSW field have ushered in automated machines and precise process control. These advancements have further optimised the use of FSW in manufacturing. Case studies conducted by TWI have been instrumental in showcasing the successes and learnings from the application of FSW across various industries. A clear window into these studies offers insights into overcoming technical challenges in FSW implementation. With the right solutions, these challenges can be surmounted for successful integration of FSW into the manufacturing process. The use of FSW in manufacturing is a testament to the method's adaptability and efficacy. By adopting FSW, manufacturers can streamline their operations for enhanced efficiency and productivity. Thus, the right choice of FSW equipment plays a pivotal role in manufacturing success.